Target Distribution Center in Charlotte NC: A Comprehensive Overview
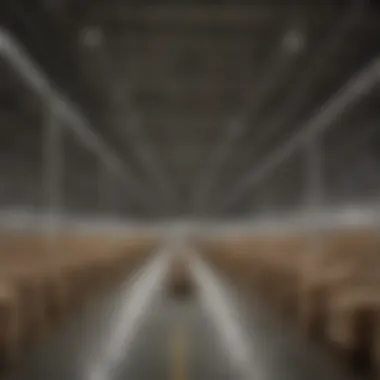
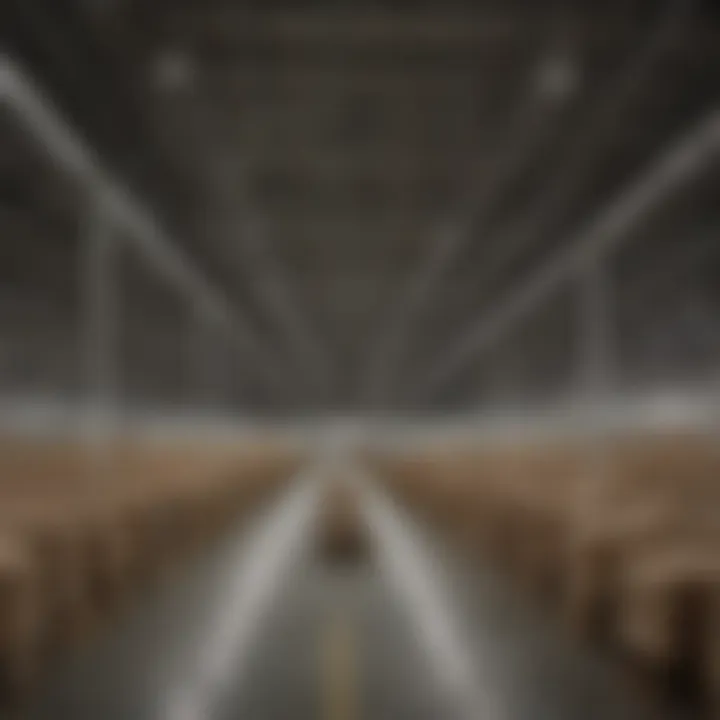
Intro
The Target Distribution Center located in Charlotte, North Carolina represents a significant hub within the intricate web of modern logistics. This facility operates at the heart of a broader supply chain, ensuring that goods move efficiently from manufacturers to retail locations across the region. For many, the implications of such a center extend beyond logistics; they touch on local economies, job opportunities, and even environmental responsibilities.
Understanding the various dimensions of this distribution center is crucial. It is not just a warehouse but a dynamic operation that engages with pest management, societal contributions, and ecological practices. By examining these aspects comprehensively, we can appreciate both the operations behind this facility and its broader impact on the Charlotte area. The following sections will delve deeper into these critical components.
Overview of Target Distribution Centers
Understanding the role of Target distribution centers is crucial for grasping the logistics framework in the modern retail environment. These centers serve as vital hubs in the supply chain, processing and distributing products efficiently while ensuring that local stores are well-stocked. The focus on these centers reveals important insights into logistics management, operational efficiencies, and the broader economic impact on regions like Charlotte, North Carolina.
Purpose and Function
Target distribution centers play numerous pivotal roles in the retail supply chain. Primarily, they function as storage facilities where a wide array of products are kept before they are shipped to retail locations. This process ensures a smooth flow of items and timely replenishment of stock on shelves.
The centers also facilitate inventory management, allowing for the organization of goods. They enable Target to optimize its supply chain operations by reducing lead times between procurement and actual sales. This efficiency is critical in todayβs fast-paced retail environment, where customer preferences can shift rapidly.
Additionally, distribution centers support logistical planning by managing transportation needs. They coordinate the movement of goods from suppliers to stores, balancing costs and delivery times. Such smooth operations ultimately enhance customer satisfaction, making target distribution centers indispensable to Target's commercial success.
History of Target Distribution Centers
The history of Target distribution centers is intertwined with the evolution of the company itself. Initially, Target operated with a simpler distribution model. However, as the retail landscape changed in the late 20th century, so too did Target's approach to logistics.
In the 1980s, as the company expanded, there was a clear need for more strategic and centralized distribution strategies. This led to the establishment of the first large-scale distribution center in the late 1980s. Over the years, the number of distribution centers has increased significantly. Each facility has implemented advanced technologies to support operations and streamline processes.
By investing in automation and efficient logistics systems, Target has been able to maintain competitiveness in retail. Today, Target operates numerous centers across the United States, with the Charlotte facility being a significant player in its logistics strategy, reflecting the companyβs commitment to growth and adaptability in a challenging market.
Location and Significance of the Charlotte NC Center
The Charlotte, NC Target Distribution Center holds substantial relevance within the overall framework of Target's logistics operations. Located strategically within the southeastern United States, the center leverages geographic advantages that enhance both efficiency and cost-effectiveness. This section will delve into the specific elements that render this center significant not just for Target, but also for the broader supply chain ecosystem in the region. Understanding these advantages can provide valuable insights into the operational strategies at play.
Geographic Advantages
The geographical positioning of the Charlotte Distribution Center is critical. Charlotte's accessibility to major highways, including Interstate 77 and Interstate 85, facilitates smooth transportation of goods. This location enables swift distribution to various retail locations across the Southeast. It reduces transit times, which is a key factor for businesses striving to meet customer demands promptly.
- The proximity to the Charlotte Douglas International Airport also plays a vital role. It allows for quick air freight options when expedited shipping becomes necessary.
- Additionally, being in Charlotte means access to a skilled labor market. Numerous logistics and supply chain professionals are available, fostering a well-trained workforce that can support operations effectively.
These geographic advantages contribute to enhancing Target's operational efficiency and cost management, which are central to any successful supply chain strategy.
Role in Target's Supply Chain
The Target Distribution Center in Charlotte functions as a linchpin in replenishing stock for numerous stores in the region. It integrates seamlessly with Target's overall supply chain strategy, ensuring that products reach customers promptly.
- Inventory Management: The center employs advanced inventory management systems that track goods in real-time. This minimizes losses and ensures that popular items are always in stock, addressing consumer demands swiftly.
- Impact on Logistics: Of notable mention is how this center influences logistics. By consolidating shipments going to various locations, Target can decrease transportation costs. Fewer trips result in lower fuel costs and carbon emissions, aligning with sustainability goals.
- Flexibility in Distribution: The Charlotte facility also allows for flexibility in distribution methods. It enables Target to adapt quickly to market changes and customer preferences, maintaining a competitive edge in the retail space.
Overall, the operational significance of the Charlotte Distribution Center within Target's supply chain cannot be overstated. Its strategic location and functional role contribute substantially to Target's ability to serve its customers effectively and efficiently.
Operational Framework
The operational framework of the Target distribution center in Charlotte plays a critical role in ensuring efficiency and effectiveness in logistics. A well-structured operational framework influences how goods flow through the center, how employees interact with technology, and how inventory is managed. This framework is crucial for responding to the increasing demand for fast and accurate deliveries. It not only streamlines processes but also enhances productivity.
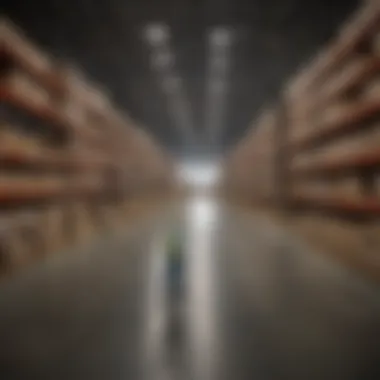
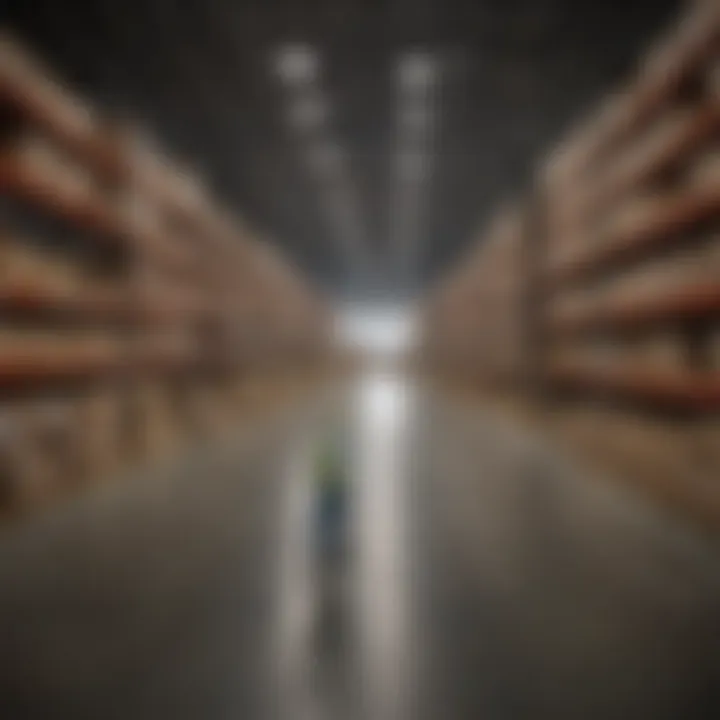
Logistics and Management
Logistics management encompasses the planning and execution of the movement of goods and services from the point of origin to the point of consumption. At the Charlotte distribution center, logistics is carefully designed to minimize delays and optimize resources. Effective logistics ensure that deliveries are timely and meet customer expectations, which is critical for maintaining Target's competitive edge in retail.
A robust logistics system includes:
- Transportation Management: Coordinating the movement of products to and from the center.
- Warehouse Operations: Utilizing space efficiently to store and retrieve items swiftly.
- Supply Chain Coordination: Engaging with suppliers and partners to fortify the entire supply chain.
Management teams monitor these logistics processes to identify bottlenecks and implement solutions that enhance overall performance. This real-time oversight allows for adjustments that are necessary in response to market demands.
Technology Utilization
Technology plays an increasingly vital role in the operational framework of the Target distribution center. Automated systems are embedded within various processes to enhance accuracy and speed. For instance, barcode scanning technology helps in tracking inventory, ensuring that every package is accounted for throughout its journey.
Moreover, advanced software systems utilized for:
- Stock Level Monitoring: Keeping track of inventory to make informed restocking decisions.
- Data Analytics: Evaluating performance metrics to guide strategic decisions.
- Transportation Logistics: Optimizing shipping routes to reduce costs and delivery times.
The use of technology not only improves operational efficiency but also allows employees to focus on higher-level tasks, thereby increasing job satisfaction and productivity.
Inventory Management Strategies
Effective inventory management strategies are essential in a distribution center like the one in Charlotte. These strategies directly impact the center's ability to respond to customer needs swiftly. By using just-in-time inventory practices, Target can minimize excess stock while ensuring that popular items remain available for distribution.
Several techniques are employed, such as:
- Inventory Rotation: Ensuring older stock is sold first to reduce waste.
- Demand Forecasting: Predicting future inventory needs based on sales trends.
- Cycle Counting: Regularly counting selected inventory items to maintain accurate records.
These strategies not only optimize storage but also improve cash flow and reduce losses associated with unsold products. With a clear understanding of inventory levels and demands, the Charlotte distribution center can maintain a steady flow of goods, which is integral to supporting Targetβs broader supply chain goals.
Economic Impact on Charlotte
The Target Distribution Center in Charlotte plays a critical role in the economic landscape of the city. This facility not only enhances the logistics network but also contributes significantly to the local economy. Understanding its economic impact involves analyzing employment opportunities and the broader contributions to local businesses.
Employment Opportunities
The establishment of the Target Distribution Center has created numerous job opportunities for residents in Charlotte and surrounding areas. The center employs a variety of roles, ranging from warehouse management to logistics coordination. Here are some key aspects:
- Job Creation: The center has established hundreds of jobs, which include both full-time and part-time positions. This is crucial for a growing city like Charlotte, which thrives on diverse employment avenues.
- Wages and Benefits: Positions at the distribution center often come with competitive wages and benefits packages. This can significantly elevate the living standards of working families in the area.
- Training and Development: Target often invests in the training of its employees. This allows workers to gain valuable skills that can promote career advancement in the logistics and retail industries.
In essence, the Distribution Center serves as a vital source of economic stability for many families. Its presence helps to reduce unemployment rates and foster community development.
Contribution to Local Business
Beyond employment, the Target Distribution Center significantly bolsters local businesses in Charlotte. Its operational framework and large-scale logistics operations create various opportunities:
- Supply Chain Partnerships: Local suppliers and vendors benefit from the distribution center's need for goods and services. This can include everything from packaging materials to maintenance services.
- Economic Multiplier Effect: When employees earn wages and spend in local shops, this initiates a multiplier effect, boosting the economy further. Local restaurants, grocery stores, and retail outlets see increased patronage as jobs are created in the district.
- Community Investments: Target often participates in community programs. This involvement helps support local initiatives and improves corporate responsibility perception within the community.
"The significance of the Target Distribution Center extends beyond mere logistics; it is a bedrock of economic growth for Charlotte, providing a parade of benefits for the local populace."
Environmental Considerations
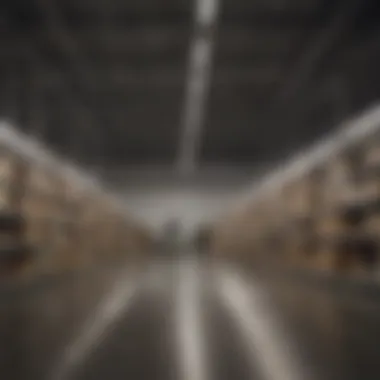
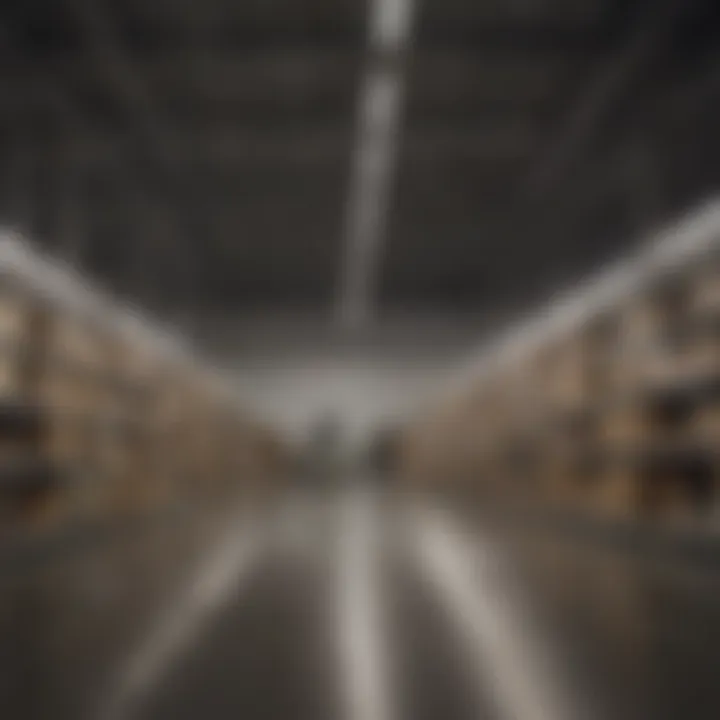
Understanding environmental considerations in the context of Target's distribution center in Charlotte, North Carolina, is crucial for a number of reasons. These practices not only enhance operational efficiency but also reflect a commitment to social responsibility and sustainable development within the logistics sector. Target has made significant strides to minimize its environmental impact while ensuring that the center meets regulatory requirements and aligns with modern sustainability goals.
Sustainability Practices
Target's commitment to sustainability is evident in various initiatives implemented at the Charlotte distribution center. These practices focus on reducing carbon footprints and conserving resources while promoting a healthier work environment.
Some key sustainability practices include:
- Energy Efficiency: The center utilizes energy-efficient systems, including LED lighting and advanced HVAC systems, to reduce overall energy consumption.
- Renewable Energy Sources: Target has invested in solar power systems to complement traditional energy sources. These initiatives contribute to minimizing dependency on fossil fuels.
- Water Conservation: Water conservation efforts are evident with rainwater harvesting systems and efficient irrigation methods, which reduce water waste.
- Green Building Standards: The facility adheres to sustainable building certifications such as LEED (Leadership in Energy and Environmental Design), promoting environmentally responsible architecture.
These efforts result in decreased operating costs and improved public perception by demonstrating Target's commitment to environmentally friendly practices.
Waste Management Systems
Effective waste management is another critical aspect of environmental considerations at the Target distribution center. The facility employs comprehensive waste management strategies to minimize waste production and promote recycling.
Some of the waste management systems include:
- Recycling Programs: The center implements robust recycling initiatives for cardboard, plastics, and other materials. This minimizes landfill contributions and encourages responsible disposal practices.
- Composting: Organic waste from onsite food facilities can be composted, reducing the volume of waste that ends up in landfills and providing nutrient-rich soil for local agriculture.
- Waste Audits: Regular waste audits help identify areas for improvement in waste reduction and recycling efforts. Such assessments allow for continual enhancement of the waste management process.
- Partnerships: Collaborations with local waste management vendors ensure the disposal of hazardous materials complies with environmental regulations.
Through these waste management systems, the Target distribution center reflects a proactive approach to waste reduction, reducing environmental impact while contributing to community sustainability.
In summary, environmental considerations are integral to the Target distribution center in Charlotte. By prioritizing sustainability practices and effective waste management systems, the facility minimizes its environmental footprint, demonstrating a commitment to corporate social responsibility.
Pest Management Challenges
Effective pest management is critical for any distribution center. It ensures smooth operations and protects the integrity of goods stored and handled. In the context of the Target Distribution Center in Charlotte, North Carolina, addressing pest management challenges takes on a multi-faceted approach. By prioritizing this area, the facility can minimize disruptions, safeguard health, and maintain a positive environment for employees and products alike.
Understanding pest management challenges involves recognizing the types of pests that can infiltrate distribution centers, such as rodents and insects. Additionally, it requires awareness of potential health risks and the costs associated with pest infestations.
Common Pests in Distribution Centers
Pests can have a significant impact on the operation of a distribution center. The most common pests encountered in these environments include:
- Rodents: Mice and rats are frequent intruders, often attracted to food items and any waste present. They can cause structural damage and spread diseases.
- Cockroaches: Often found in warm, humid environments, cockroaches multiply rapidly and can contaminate inventory with droppings or secretions.
- Ants: Various species can invade facilities searching for food. Their colonies can grow quickly, leading to larger infestations if not managed promptly.
- Stored Product Pests: This includes beetles and moths that target dry goods and other stored products, often going unnoticed until significant damage is done.
Addressing these pests swiftly is essential to prevent them from posing risks to the operation, employees, and the products.
Integrated Pest Management Approaches
Integrated pest management (IPM) is an effective strategy for controlling pest populations while minimizing environmental impact. This approach generally comprises several key components:
- Monitoring and Inspection: Regular inspections help identify pest presence early. It involves checking areas prone to infestations, such as storage spaces and entry points.
- Prevention: This step can include physical barriers, sealing gaps, and proper waste disposal practices. Maintaining cleanliness reduces the attraction of pests to the facility.
- Thresholds: Establishing action thresholds based on pest population levels helps determine when interventions are necessary. This prevents unnecessary use of control methods.
- Control Measures: These can be either chemical and non-chemical. Non-chemical methods could include traps or exclusion tactics, while chemical options should be used judiciously and as a last resort.
- Evaluation and Reevaluation: Regular assessments of pest control measures ensure their effectiveness and allow for adjustments based on changing circumstances.
Successful pest management is not only about elimination; itβs also about understanding and preventing future infestations.
In summary, the approach to pest management at the Target Distribution Center requires diligence and adaptability. By employing integrated pest management practices, the center can maintain a safe and efficient operational environment.
Health and Safety Regulations
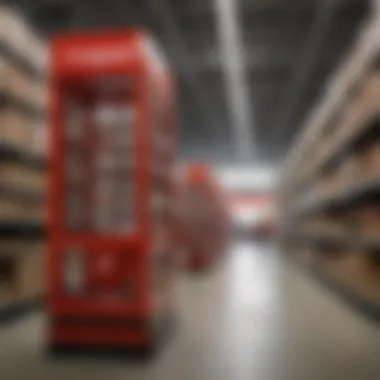
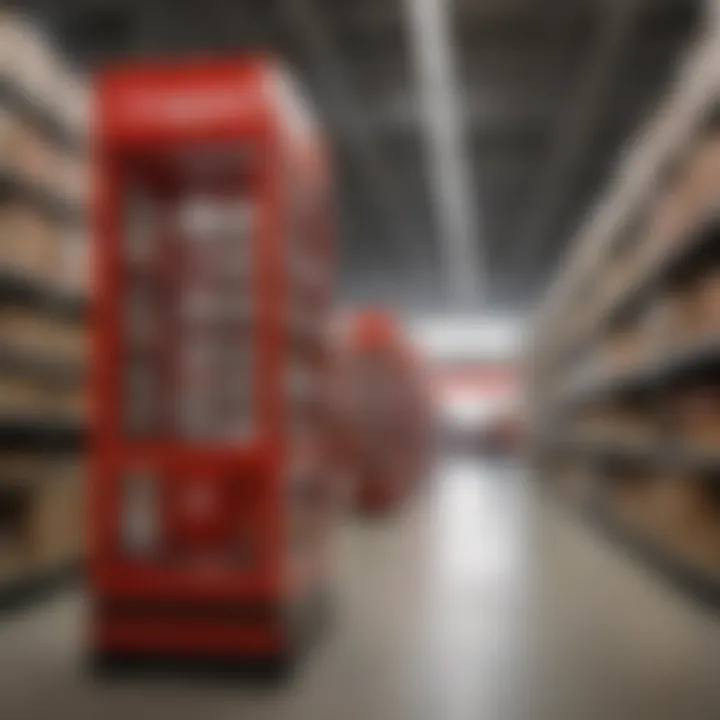
Health and safety regulations are paramount in any distribution center, and the Target distribution center in Charlotte, NC is no exception. These regulations ensure that the workplace environment is safe for all employees and adheres to industry standards. The importance of these regulations cannot be overstated. They not only protect employees but also enhance overall operational efficiency and productivity by minimizing accidents and injuries. Furthermore, compliance with regulations can safeguard against legal repercussions and promote a positive corporate image.
Compliance Requirements
Compliance with health and safety regulations involves several key elements. The Target distribution center must adhere to federal, state, and local regulations to ensure safety protocols are established and followed. This compliance typically includes:
- OSHA Standards: Adhering to the Occupational Safety and Health Administration standards is essential. This includes regular safety training and reporting procedures for any incidents.
- Regular Inspections: Routine safety inspections are vital to identify potential hazards. These inspections can help in addressing issues before they lead to accidents.
- Documentation: Keeping thorough documentation of safety practices and incidents is required. This ensures accountability and provides data for ongoing safety improvements.
By meeting these compliance requirements, the Target distribution center fosters a culture of safety, which is beneficial for both employees and the organization.
Employee Safety Protocols
Employee safety protocols are another essential aspect of health and safety regulations in the Target distribution center. Implementing effective protocols not only ensures a safe working environment but also boosts morale among employees. Some core safety protocols include:
- Training Programs: Regular safety training for employees is crucial. These programs typically cover equipment handling, emergency procedures, and proper use of personal protective equipment.
- Emergency Plans: Having clear emergency procedures in place is necessary for any urgent situations. Employees should be familiar with evacuation routes and emergency contacts.
- Reporting Procedures: A straightforward reporting system for safety hazards or incidents encourages employees to voice concerns without fear. This proactive approach allows for immediate action to mitigate risks.
"Safety does not happen by accident. It requires planning, intent, and execution."
In summary, maintaining health and safety regulations is vital in the Target distribution center in Charlotte, NC. Compliance ensures a safe working environment, while effective employee safety protocols promote a culture of safety and well-being. This comprehensive approach not only protects employees but also contributes to the center's operational efficiency.
Future Outlook
The future outlook of the Target Distribution Center in Charlotte, North Carolina, represents a critical aspect of the company's ongoing commitment to optimizing its logistics capabilities. Understanding the components involved in this outlook provides valuable context for various stakeholders. The nuances of expansion plans and evolving supply chain dynamics will be significant for the center's operational strategy and success moving forward.
Expansion Plans
Target has laid out ambitious expansion plans for its distribution center in Charlotte. The intention is to increase its capacity to meet growing demand across the Southeast region. This expansion includes the addition of new automation technologies, which are pivotal in enhancing efficiency in operations.
Potential benefits of the expansion include:
- Increased storage space: This allows for better product availability and quicker fulfillment times.
- Job creation: As the facility expands, new positions will surface, contributing to economic growth in the Charlotte area.
- Enhanced logistics: With updated technology and infrastructure, the center can manage an increased volume of products seamlessly.
As part of this expansion, Target also emphasizes sustainability. New energy-efficient systems are expected to be implemented, reducing the facility's carbon footprint. The integration of eco-friendly practices will help align with the overall corporate goals surrounding sustainability.
Evolving Supply Chain Dynamics
Changes in the supply chain landscape present both challenges and opportunities for distribution centers like the one in Charlotte. The continuous evolution in consumer behavior, especially the shift towards online shopping, influences how Target structures its logistics.
Key considerations of evolving dynamics include:
- Technological advancements: Automation and artificial intelligence are at the forefront of improving logistics operations. Target seeks to incorporate these technologies to enhance efficiency and accuracy.
- Demand forecasting: Enhanced data analytics will support better prediction of consumer trends, allowing for more effective inventory management. As consumer preferences fluctuate, agile responses become necessary.
- Resilience: The pandemic underscored the importance of having resilient supply chains. Target is likely to invest in strategies that bolster its ability to adapt swiftly to market changes and disruptions.
"Understanding the evolution of supply chain dynamics is essential for ensuring the long-term viability of distribution centers. Adaptability will be key to sustaining operations in a fast-paced market."
In summary, the future outlook for the Charlotte distribution center is built on the pillars of expansion and adaptability. As Target navigates these trends, the implications for local employment and economic health remain significant.
Ending
Understanding the Charlotte distribution center of Target is essential for grasping the broader logistics ecosystem. This facility serves as a crucial component in Target's supply chain, influencing various aspects such as operational efficiency and environmental stewardship.
Key Takeaways
- Operational Efficiency: The distribution center streamlines supply chain processes, ensuring timely delivery of goods.
- Economic Contribution: It boosts local employment and supports surrounding businesses, creating a more vibrant economy.
- Pest Management and Safety: The facility implements integrated pest management and complies with health regulations, safeguarding employee welfare.
Implications for Stakeholders
The insights gained from the operations at the Charlotte distribution center extend to multiple stakeholders. Local businesses can find opportunities for partnerships, while employees benefit from stable jobs within a robust framework. For policymakers, supporting such facilities could align with regional economic goals.